

Tool & Die Components:













Work Holding Components:




Materials Handling:




Lubricators:


| |
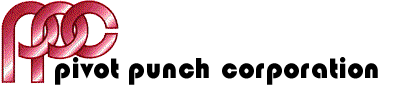
Pivot Punch Corporation is one
of the world's largest manufacturers of punches, die buttons, retainers and
custom made tools for the stamping and forming industry.
All Pivot punches are manufactured
in the USA.
To see Pivot's range of punch
forms click here.
TONDRA-GENIC™
TREATMENT |
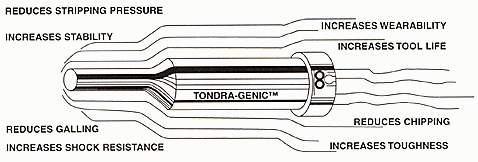 |
Pivot Punch
Corporation is introducing TONDRA-GENIC™ TREATMENT which is a
new process that can be applied to all of our high speed tool
steel products.
TONDRA-GENIC™
TREATMENT is a unique combination of two processes, Pivot's
exclusive Tondra treatment and a specially controlled
cryogenic treatment.
The Tondra
Treatment portion of this new process produces an extremely hard
case of 72-75 Rockwell for the ultimate in resistance to
abrasion, firing, and galling. This process also adds lubricity
to the surface which reduces stripping pressure. The cryogenic
treatment portion produces maximum tool hardness and stability
which results in greater toughness and shock resisting quality.
When TONDRA-GENIC™
is applied to piercing tools a 600% increase in tool life is not
uncommon.For increased productivity specify TONDRA-GENIC™
TREATMENT on your next order from Pivot.
|
Coatings |
Titanium Nitride (TIN)
Is an excellent general purpose coating for punches and dies to
protect your tools from wear. TIN is a good choice for wear
parts requiring resistance to abrasive and adhesive wear.
(This coating is recognized by its gold appearance.)
Titanium
Carbonitride (TICN)
Is a high performance coating for forming and punching tools
that encounter excessive mechanically stressed cutting and
forming edges, and were high speed and feed rates are desired.
(This coating is recognized by its blue gray appearance.)
Hard Lube
Is a specialized multi layered coating. The base is a wear
protective coating that is covered with a lubricative outer
layer. This coating is most beneficial in forming operations.
(This coating is recognized by its black gray appearance.)
|
Steel Comparisons |
Pivot
PM 1O steel punches and dies take advantage of the unique
properties of this Crucible Particle Metallurgy steel. It is
designed with a tough, air hardening base analysis with added
high carbon and vanadium. This provides PM 1O with a combination
of exceptionally good wear resistance, toughness and strength
for cold and warm work applications.
|
New
grades: PM 3 and PM 15
-
PM 3 - great toughness
-
Toughness approaching S7
-
Wear resistance greater than M2
-
Use for impact situations instead of S7, for high
toughness without giving up wear or coatability
-
PM 15 - great wear
-
50% - 100% longer wear life than PM 10
-
Same hardness, heat treatment as PM 10
-
Wear upgrade from PM 10, or replace FerroTiC, or use
where carbide is too brittle
|
Wear Resistance |
|
Impact Strength |
Steel |
Hardness (HRC) |
Wear Resistance* |
Steel |
Hardness (HRC) |
Charpy C-Notch* Impact Value (ft.-lb.) |
PM 15 |
62 |
125 |
PM 15 |
62 |
10 |
PM 10 |
63 |
90 |
PM 10 |
63 |
15 |
PM 10 |
60 |
75 |
PM 10 |
60 |
25 |
D2 |
62 |
10 |
D2 |
62 |
17 |
M2 |
62 |
17 |
M2 |
62 |
17 |
PM M4 |
64 |
31 |
PM M4 |
63 |
30 |
A2 |
60 |
5 |
A2 |
60 |
36 |
PM 3 |
60 |
22 |
PM 3 |
60 |
75 |
S7 |
57 |
2 |
S7 |
57 |
108 |
*Reciprocal of the
wear rate in unlubricated crossed-cylinder wear test in contact
with rotating tungsten carbide cylinder. |
*Standard size
Charpy Test specimen and notch depth with ½ inch notch radius. |
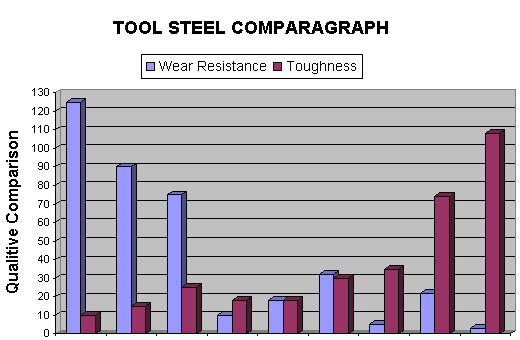
GRADE |
PM 15 |
PM 10 |
PM 10 |
D2 |
M2 |
PM M4 |
A2 |
PM 3 |
S7 |
HRC |
62 |
63 |
60 |
62 |
62 |
64 |
60 |
60 |
57 |
Note: This information is to
be used as a guideline for material selection to help solve your
punching requirements. |
|
For enquiries, Contact GW Technologies
here.
|